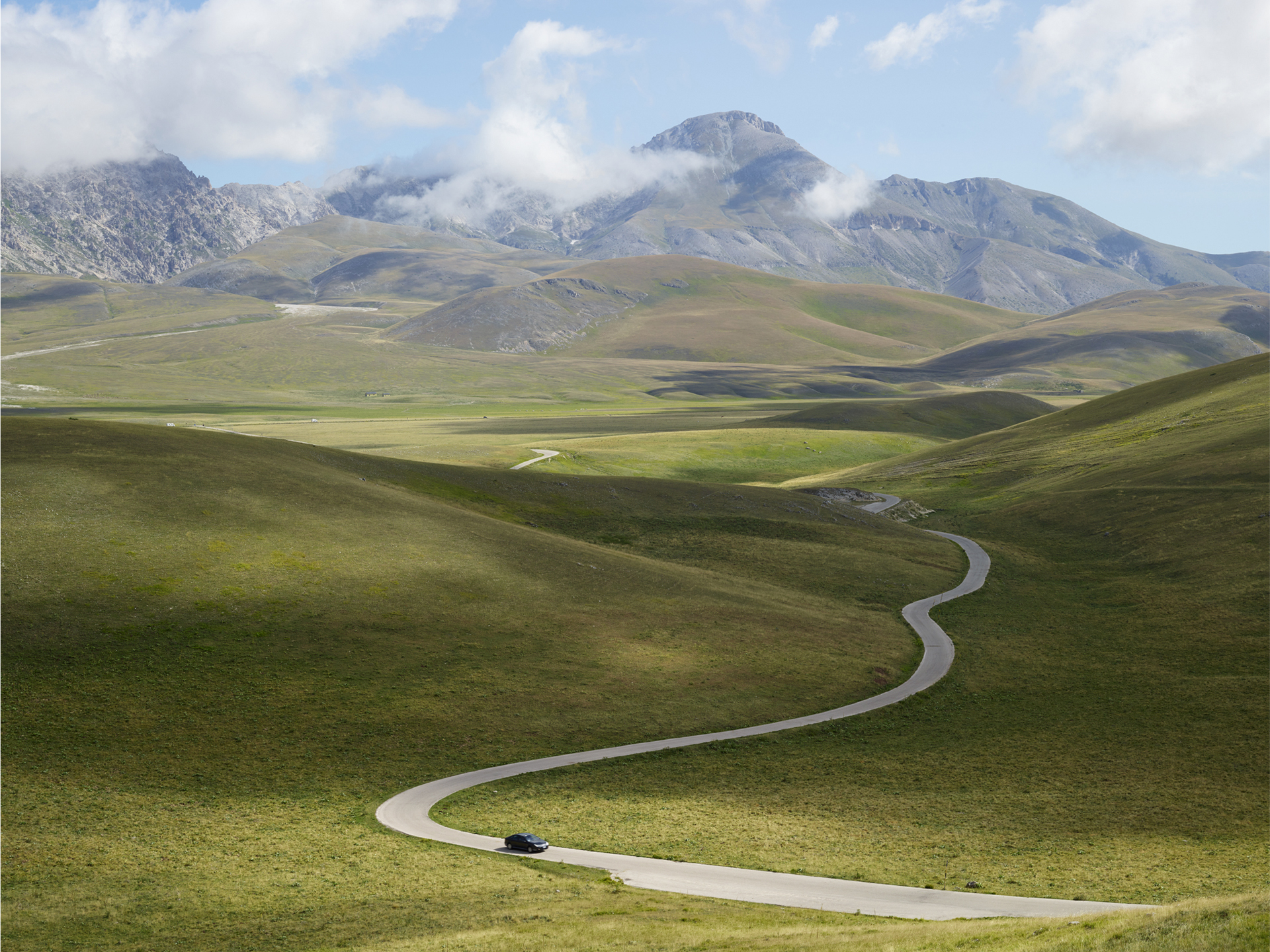
環境への取り組み
マテリアリティ
地球温暖化防止
大気汚染防止/環境負荷物質削減
資源有効利用
水資源の保全
関連するSDGs
取り組み事例
浜名湖クリーン作戦(主催:湖西市・浜松市)への参加
おうちdeグリーンカーテンコンテスト
有害なガソリン蒸気の放出を抑制
日本を始めとしたさまざまな国で、地球環境保護のためにエバポ規制があります。
当社では、こうした規制に対応するため、有害なガソリン蒸気(HC)の大気への放出を防ぐための製品を生産し、地球環境保護に貢献しています。
油圧制御で低燃費に貢献
当社では、オートマチックトランスミッションの油の流れの切り替えを行うON/OFFソレノイドのトップランナーとして、製品を世に送り出しています。
●自動車の変速を自動で行い、スムーズな走りで利便性を向上
●変速制御の多段化による低燃費かつ、業界最小のソレノイドで省資源に貢献
●パーキング制御により安心・安全な運転を支援
成形廃材再利用
-
製品設計段階から端材のリサイクルを考慮した工程設計を行っています。
-
設備高速化で設備数を減らす
-
-
設備数減:溶接装置を軽量化、高速サーボモータ採用し高速化しています。
エネルギー安定供給で効率的な運転
安定供給を維持するため、平日は日常点検、生産が止まっている休日や連休には電気設備、エア供給設備の定期点検、冷却塔清掃などを行っています。
日常点検(毎日:800項目)
エネルギー供給設備(電気、エア、水)の日常点検項目数は本社・吉美あわせて約800項目もあり毎日点検を行っています。
定期点検(509項目)
例えば、エア供給設備では冷却機5台、圧縮機17台、ドライヤ11台、フィルタ8台、エアタンク1台の点検項目の合計が509項目にもなります。
※2022年からDX化により点検作業にタブレットを運用し作業性を向上させています。
冷却塔清掃(2/Y:12台)
冷却塔内部の熱交換器に汚れが付着すると、熱交換効率の低下となるために生産がない休日に雨合羽を着用して水の飛散を受けながら清掃しています。
吉美工場排水処理(生活系)の公害防止
-
脱窒槽清掃
-
死骸を網ですくい除去
「排水の水質分析」で浜名湖を守る
工場長現認会・交流会
-
「安全最優先」
各工場で毎週開催して困り事の吸上げと横串しを行い安全意識の浸透させる、本社・吉美工場を新しい目で相互研鑽で気づきを与えて学び交流を深めて活性化を推進しています。
週に1回、5グループで本社工場、吉美工場の係単位で実施しており、本音で言い合いながら確認する事で、理解させて正しい事をやる風土を構築します。 -
継続的改善活動
-
-
職場内のムリムラムダの問題点を抽出して、自分達で出来る事から改善を学び達成感を共有して成長につなげています。
活動事例:経費削減「手袋再利用化」・・・使えるのに捨てるのはもったいない
手袋購入金額 △約60%低減
エネルギー使用量を減らす設備設計
-
ハイサイクル・多品種対応、省エネの熱硬化成形機を開発
新たな技術を開発し、環境にやさしい設備づくりを推進しています。
-
加工工程で発生する廃材の有効利用
-
-
部品加工で使用するワイヤ加工機の工具(使用済みワイヤ)再生化
使用済みワイヤをリサイクル化し、資源有効利用を推進しています。
『資源のムダ使い』を無くして地球を次世代に繋ぐ
-
技術を自在に操り考え抜いたパッケージで、『ムリ・ムダ・ムラないモノ運び』を可能にし、『資源のムダ使い』を無くして地球を次世代に繋ぎます。
-
帳票検索&照合システム開発(内製)
-
-
社内の梱包工程において、関係会社をベンチマークし、各種帳票の検索及び機械照合を内製で開発・導入を実施し、品質保証度のランクUPと作業要領書とチェックシートのデジタル化によるペーパーレスを推進しています。
環境負荷・CO2排出量をミニマム化する要素技術開発
デジタル化によるペーパーレス
エネルギーロス低減
-
エネルギーのロスを見えるようにし、省エネ改善ができるしくみを設置
省エネロス低減を加速させる為、エネルギーの見える化を推進しています。
-
廃棄物低減
2000年より廃棄物のリサイクル化を推進し、2002年5月 「ゼロエミッション」を達成しました。現在は廃棄物の低減活動、及びサーマルリサイクルから資源リサイクル化への転換等推進しています。
PEF活動(全社的省エネ活動)
デンソーグループとして一体となった省エネルギー活動を展開・推進して地球温暖化防止対策に努めています。
省エネ活動内容
・空調機省エネ活動
・休日設備の電源OFF活動
・成形機・恒温槽・リフロー炉断熱改善
・成形機材料乾燥機断熱改善
・インバーター方式による改善
・エアーブロウ間欠化改善
・エアー漏れ改善活動
・事務局による省エネパトロール
クリーンエネルギー導入2008年度
クリーンエネルギーによるCO2削減に取り組んでいます。
太陽光で発電された電力は、当社で使用されるパソコンとサーバーに使用されています。
-
エアー漏れ改善活動
「エアー漏れ体感機コーナー」では、触感・音でエアー漏れ量を体感します。現場で、エネルギーのムダとなるエアー漏れを探し当てる事が可能となり、エアー漏れ改善活動につながります。
-
-
-
硬化用連続炉断熱改善事例
硬化用連続炉を断熱することにより、熱効率を上げCO2低減を行います。(実績:CO2削減量:0.72t-CO2/年)